Smart manufacturing is a digitalisation strategy that aims at end-to-end integration of manufacturing operations using Industry 4.0 technologies to enable a flexible and dynamic environment for delivering smart products to modern-day consumers. We see an increasing number of electronics companies going for smart manufacturing due to the growing demand for new electronic products that can meet customer expectations.
Nikhil Pal, digital manufacturing expert, Jabil, says, “Products are becoming complex with new features and components day-by-day in every industry. Traditionally, customers used to look at us only for quality, cost, and delivery. Now they look in terms of agility too, that is, how fast we can respond to the customer demand fluctuation. For example, we are not making the same smartphone model for many years to come.”
According to a market report from Grand View Research, the global smart manufacturing market size was valued at 215.8 billion dollars in 2019 and is expected to grow at a CAGR of 11.8 per cent in the forecast period 2020 to 2027.
The answer to this is simple—getting better products at lower costs. Ability to use manufacturing data and automation to incorporate minute product variations without having to reassemble equipment provides flexibility in the production process. The manufacturers can thus produce customised products at reduced downtime and better efficiency. Manufacturing processes will be better; for instance, failure detection using automated optical inspection (AOI) can be done based on images. The main benefit of smart manufacturing is that investment, if done right, can decrease manufacturing costs significantly.
Today’s quality-conscious customers want to know everything, from design to production. They develop a sense of confidence from the awareness that they are purchasing good quality products. Shrikant Sharadrao Borkar, founder, SSB Technocrat, says, “Customers want transparency in the process. With smart equipment, data can be shared in real time. The customer will be happy to interact, and for any changes, he/she can see the process remotely. This will encourage customers to interact at your end.”
Talking about the benefits for manufacturers, Nikhil Pal says, “When we are using smart manufacturing initiatives for digital transformation, we are able to link the vendors in the digital supply chain. We get an overview of the vendor to the end customer. End-to-end visibility in the entire supply-value chain because of digitalisation allows us to see even the inventory level so that the focus is to better the efficiency, productivity and also minimise the inventory holding in our factories.”
Overall, this is a win-win situation for both manufacturers and customers. When customers know that the manufacturer is using smart manufacturing technology/equipment for manufacturing, it increases their trust and satisfaction, which enhances the brand value for the business in the long run. When machines are better in terms of speed, size, and capability, even workers will benefit.
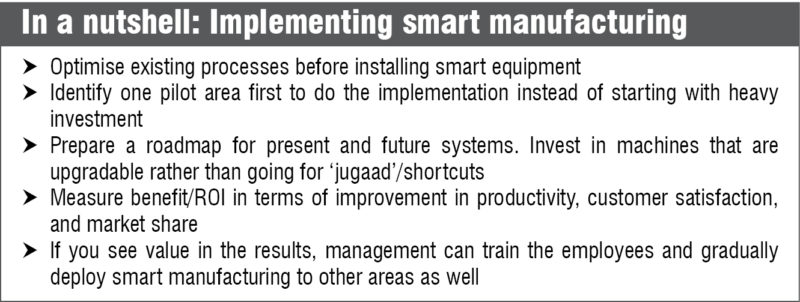
Challenges that need to be dealt with
Companies realising the benefits of smart manufacturing and wanting to improve their work efficiency often find themselves stuck in the early stages of adoption. MSMEs are the backbone of an economy, but the implementation of smart manufacturing in India is slower because of a lack of motivation in MSMEs.
Shrikant Sharadrao Borkar says, “Adoption is low for SMEs due to inadequate infrastructure, use of refurbished machinery, and inability to justify ROI. However, the adoption rate might increase due to customer demand and globalisation requirements.”
Due to the lack of adequate budget, companies tend to go for options that may not be fail-safe for the entire system, from design to production in the long run. The inability to justify ROI arises from the fact that traditionally companies follow the wrong approach of measuring automation benefits against a reduction in workforce.
Besides, there is a huge skill gap that acts as an impediment to the growth of the manufacturing sector, according to Industry Pulse: 2018 Manufacturing Workforce Report by Tooling U-SME, a provider of manufacturing training solutions.
Another challenge is intellectual property (IP) protection, that is, how are businesses going to keep proprietary data in smart factories. Roberto Gatti, CEO, Delvitech SA, says, “Customers need access to the systems like the data collection system in the manufacturing plant to know the ongoing status of production. The amount of data coming in and going out will be huge, which requires proper infrastructure. At the same time, the privacy of individual customers is at risk if data in the manufacturing plant is not taken care of.”
Current adoption scenario
There has been a big push for Industry 4.0 in the last ten years. Even though there is growing adoption of smart manufacturing worldwide, the market size varies considerably from one region to another.
Germany is projected to have the largest smart factory market share in the European region in the next five years based on a report from Global Market Insights. The report also states the current dominance of North America; the continent’s smart factory market was valued at around thirteen billion dollars in 2018.
A significant portion of smart manufacturing companies is present in the Indo-Pacific region that includes countries like Japan, South Korea, Taiwan, and China. According to an IDC study, industrial companies across the region are undergoing a rapid digital transformation, adding 1.16 trillion dollars to Indo-Pacific GDP and boosting annual growth rates by 0.8 per cent. In Singapore, the government has come out with a smart industry readiness index (SIRI). They assess all industries based on this assessment. This is helping the government and companies in identifying how to start, scale, and sustain their transformation.”
Yet, adoption in India is still low as compared to other countries, and manufacturers show a lack of interest in smart manufacturing. However, government initiatives like Smart Advanced Manufacturing and Rapid Transformation Hub (SAMARTH) Udyog Bharat 4.0 that aims to create awareness and integrate Industry 4.0 technologies in the Indian manufacturing sector for large organisations as well as MSMEs have a positive influence on the market. In the last three years since the operation, tax reform rolled out in the form of the Goods and Services Tax (GST) has had a huge impact on supply chains.
Countries can come together to collaborate and thereby accelerate the path going forward in smart manufacturing. For example, this year, the Department of Science and Technology (DST) launched the India-Russia joint technology assessment and accelerated commercialisation programme. Such partnerships aim to help scientific and production houses, researchers, and entrepreneurs in solving the existing challenges and create globally competitive products.
How to implement smart manufacturing
According to Capgemini’s Digital Transformation Institute, some manufacturers hired consulting firms to help build a business case and roadmap, others partnered with technology providers for feasibility studies, while the rest used end-to-end technology solutions to start out with smart manufacturing.
A calculated approach involving minimum risks is necessary. A.K. Rao, AGM, NMTronics India, says, “Smart manufacturing should be implemented in a phased manner. The company should define exactly what they require. It is necessary to prepare a roadmap for present and future systems instead of taking ‘jugaad’, a common practice in India.”
Shrikant Sharadrao Borkar says, “Any party—be it from electronics, mechanical, or any other background—needs to see what’s going to change technology in the next ten years. Suppose you need a Wi-Fi network and servers, if not upgradable, we can’t choose that. If it is not adopted by people, machinery alone can’t do anything. All the HODs and other senior leaders can train the employees. People are eager to learn, so management needs to take care.”
If you have limited finances, start from the part which you think is more complicated. It is necessary to know what you want to produce and have everything from the purchase of materials to what is happening in AOI under control, and then to ensure quality.
Roberto Gatti says, “To start smart manufacturing, first have a strong infrastructure to support large amounts of data and complete integration of machines including the Internet, good servers, and software for data collection. If you have no control over what you produce, you will be compelled to accumulate a huge amount of components.”
Nikhil Pal says, “First, the management perspective needs to change. Also, we can’t just allocate budgets, identify one pilot area, and do the implementation there. After implementation, train the people and share the result with the rest of the organisation. Once you see value in that, gradually deploy to other areas as well. Don’t start with heavy investment. For example, we can use an IoT gateway to take data out from existing equipment and have our backend analyse the data. Look at how much is the reduction in downtime and quality defects, improvement in productivity, more products you can manufacture, customer satisfaction, and market share. Convert these into numbers when going for ROI calculation.”
What SMEs can do
According to a 2018 Smart Manufacturing report, manufacturers included in ‘SME’s Manufacturing in the New Industry 4.0 Era’ survey said that the top barriers preventing smart technology were lack of corporate leadership to lead or plan a smart manufacturing strategy and lack of skill set to manage implementation.
For SMEs to start implementing smart manufacturing of electronics facilities keeping finances into consideration, they need to look for possible financing, renting options, and sharing options for smart manufacturing to work. Manufacturers can aid this progress by taking the responsibility to educate their consumers about the different models based on their budget, capacity, and speed requirements so that they know what to buy. Various local solutions are available for assembly, testing, and more. SMEs can even collaborate with each other for machines. A.K. Rao says, “Different models with capacity and speed are available based on budget. Customers need to check if machines are upgradable. Sometimes they don’t know what to buy.”
Companies need to optimise their process before installing smart equipment, if they don’t have enough budget. SMEs can use existing equipment with modifications. For example, adding an IoT gateway for data processing and analysis. They can also look for renting local solutions under Atmanirbhar Bharat. Once they get revenue, they can purchase the solution. Manufacturers and sellers need to be willing in terms of financing options like accepting payments in instalments.
What happens to jobs?
Many people fear that new techniques like AI in AOI can lead to the loss of their jobs. But contrary to beliefs, even the employees can benefit from smart manufacturing. It can provide more jobs because the technologies need to be managed, controlled, maintained, and developed.
Technology is always focused on reducing repetitive work we can automate. For example, before AOI, operators used to do tedious jobs like inspecting solder joints, while now we can tell if it’s a true or false failure using pictures. People can focus on higher value-added jobs that require complex problem solving, critical thinking, creativity, which machines are not capable of right now.
Roberto Gatti says, “Manufacturing to a higher level is not removing jobs but creating more on the production side; the manufacturing process itself may not need more than a few people though. For example, repairing is usually expensive, and correcting huge numbers of errors leads to frustration in workers. Smart manufacturing equipment is helping the manufacturing process to be better and workers to be better.”
A.K. Rao says, “People are, in fact, more excited with technology. Humans can’t produce or see complex PCB assemblies. There is fatigue from repeatability. The jobs will be transformed and skills can be used on other platforms. The new generation can adapt to Make in India better as they will get an opportunity to work in a different way.”
This discussion on smart manufacturing equipment for electronics manufacturing took place during India Technology Week, September 2020. To register as a speaker, exhibitor, or audience at India Technology Week please log on to www.indiatechnologyweek.com