Digitisation in the industrial manufacturing segment is about using capacity and a properly-calibrated information-driven solution to solve problems and reduce pain-points in the enterprise.
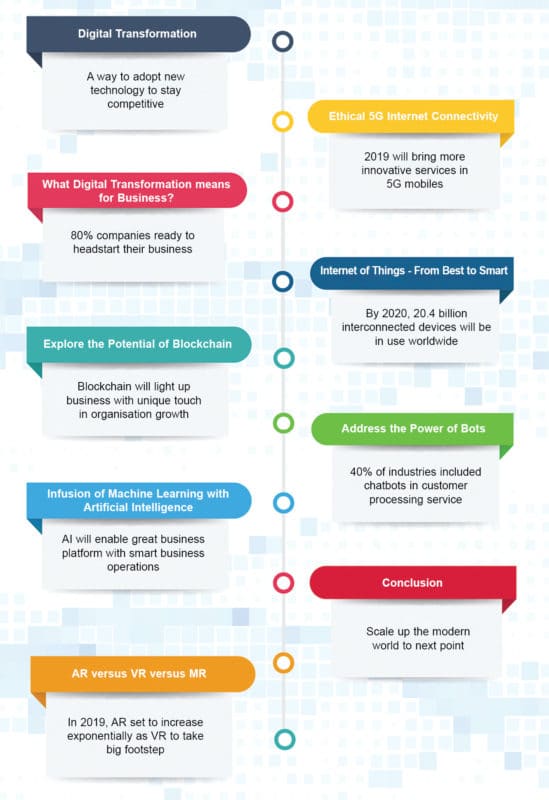
Digital transformation only makes sense if it supports an organisation’s overall strategy. Smart models of manufacturing and business are being created through collaborative and self-aware machines and processes. This has a direct impact on competitiveness and the quality of goods and services.
In the era of smart manufacturing, human beings and machines will be linked together by data networks. However, networking within production processes and across company boundaries is possible only if standards and specifications are in place that are applicable throughout the world. Self-driven businesses is the way forward for the Indian manufacturing ecosystem, and it is achievable in a manner that works for all.
Smart manufacturing began for promoting efficiency in the commercial sector, but now its potential for public benefit is increasingly being recognised. On the other hand, smart infrastructure is leading the way to a new set of economies around data gathering, decision-making and public utility technology. As world digitisation progresses, different infrastructures will have to compete with each other to achieve the fastest economic growth. The winner of this race will be the infrastructure that manages complexity of its size best. In other words, infrastructure will need to become smart to maintain its competitive advantage.
The manufacturing industry is being reshaped by the fourth industrial revolution, powered by the Internet of Things (IoT). This IoT revolution will help upgrade factories or build new systems from scratch to increase productivity and stakeholder value profoundly. Through integration of several modern technological innovations, such as advanced process control and smart panels, the concept of smart infrastructure can witness a massive overhaul in just a short period.
Opportunities for OEMs and their supply chain
Original equipment manufacturers (OEMs) can leverage augmented reality (AR) for improving workforce productivity. AR enhances users’ view of the physical world with the overlay of real-world or hypothetical digital information from IoT data, digital models, third-party data and business system information. It helps train or guide users on how to perform a task through the overlay of digital instructions or real-time expert guidance.
AR provides safety instructions, real-time transfer of knowledge and expertise through digital step-by-step instructions to guide users. Users can also manipulate digital graphics or extend a product interface through an AR interface. This enables them to expand and customise control of product functions, modify digital designs and enhance physical products with digital experiences.
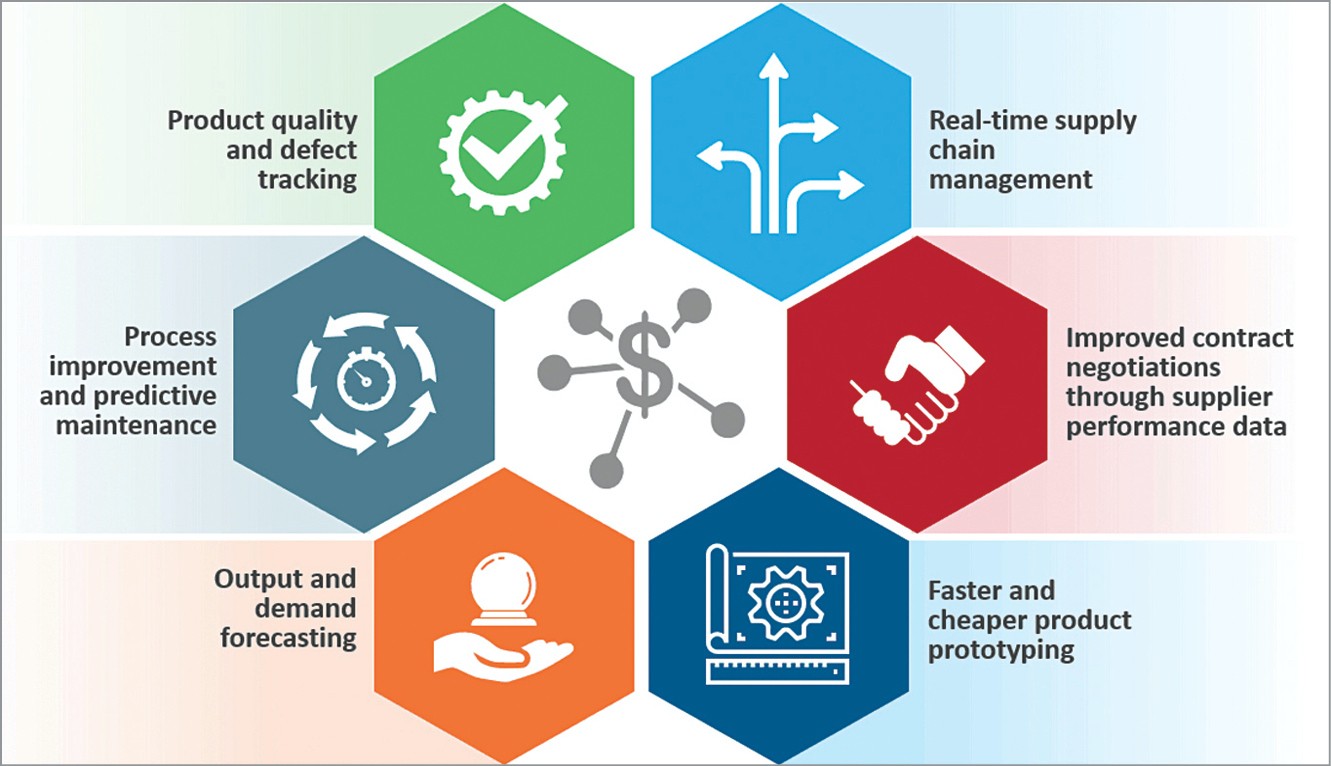
Digital transformation impacts the entire value chain in the following manner:
- Delivery and service. Personalised customer experience, outcome-based revenue models
- Corporate operations. Performance benchmarking, supply chain visibility and planning, process engineering, continuous improvement, workforce transformation
- Plant engineering. Integrated information and control systems, universal connectivity, converged information technology (IT) and operational technology (OT) networks
- Procurement. Supplier visibility, track and trace
- Maintenance and reliability. Asset health monitoring, predictive maintenance, field workforce effectiveness, environment, health and safety management
- Manufacturing operations. Shop-floor workforce flexibility and efficiency, automated touchless factory quality assurance, compliance and analytics, energy monitoring and management, real-time operational intelligence
Bridging the gap between machines and IT
Technologies that can bridge the gap between OT and IT are smart assets, multi-disciplined control and information, secure network infrastructure, mobility and scalable computing. Information-driven manufacturing leads to ease of use, better quality control, increased safety, increased productivity, improved design through simulation (CAD/CAM), energy savings, reduced labour costs, reduced or removed routine manual and clerical tasks, and so on. It requires building a collaborative team, reliable and secure infrastructure, technology upgrade for the digital world, developing skills (educating and training employees), partnerships to close the gaps and solve challenges for successful digital transformation.
Between OT and IT, there lie various manufacturing operations and management processes that help achieve a connected enterprise. OT includes materials and transport, machines and testers, controllers and scanners, and 3D printers. Whereas, IT includes ERP, financials, HR, logistics, quality and warehouse.
Smart in-line inspection systems and plant monitoring systems
Defining a problem gives half its solution. Utilising resources effectively, capitalising human resources intelligently, managing finances and deploying the right technology can solve any business problem. Trending technologies applied in Industry 4.0 are the Industrial IoT (IioT), RFID, AR and virtual reality (VR) for enhanced visualisation and learning, cyber physical systems, computer vision, 3D printing with multi-material capability, automated guided vehicles, private LTE-enabled connectivity, cobots, smart sensors, network security, implementation of OPC Unified Architecture (OPC UA, a machine-to-machine communication protocol for industrial automation), actuators and controllers, additive manufacturing, digital twins, wireless instrumentation, cybersecurity and industrial design.
A cyber physical assembly line includes the following smart machine interactions: voice interaction, WhatsApp messaging, voice calling, augmented experience using AI, machine learning, NLP and analytics, remote access to human-machine interface (HMI).
Maintenance and electrical fault finding can be achieved in four steps, as explained below.
- Design a CAD model, which is a digital replica of a physical system.
- Create an electrical schematic design. When synced with the CAD model, add electro-mech layer of information.
- Apply the IIoT. It provides data, which when analysed gives detailed information about the machine’s running state.
- Apply AR as GUI to digital data in a user-understandable format.
Preparing an enterprise for digital connectivity
All industrial revolutions have been driven by innovation and technology. For the first industrial revolution, mechanisation was the driver and steam, the enabler.
For the second industrial revolution, mass production was the driver and electricity, the enabler.
For the third revolution, PCs, connectivity and automation were the drivers and IT, the enabler.
For the fourth revolution, the IoT, artificial intelligence (AI), cloud, robotics, AR, VR, mixed reality (MR) and chatbots are the drivers, and connectivity, the enabler. The fourth industrial revolution is powered by connectivity, and has enabled expanding the scope of business-critical applications. To unlock this, it is important to become adept at controlling the physical with digital means.
Success of industrial automation depends on reliability, connectivity, distributed intelligence, transparent IT architecture, security, easy integration, flexible transport, additive manufacturing, standards and software services.
The digital value chain for Industry 4.0 can be split into seven key components, as follows:
- Machines/devices. Ecosystem-based approach, leveraging on existing deployment
- Network. Multi-access network management, proposing the best technology
- Platforms. IT infrastructure-interface enablers, platforms to nurture ubiquitous approach
- Applications. Industry-specific use-case, machine learning and analytics
- Solutions. Business ease creation, solution design and delivery
- Operations. Project implementation and support
- Project management. Maintaining network and applications uptime, periodic upgrades for security and operational improvement
Connectivity is paving the way for such industries as automotive, oil and gas, banking and finance, IT, power and production, to be ready for Industry 4.0. There are verticals like real-estate, healthcare, project development, trading, aviation and others adopting LTE in this direction.
Some industrial automation use-cases
Nokia and BSNL have collaborated for Industry 4.0, and have moved from traditional wired factory networks to wireless networks, leading to improved equipment mobility for enhanced flexibility of manufacturing infrastructure. Early adoption of IIoT applications in industries have improved productivity and operational efficiency, too.
Rockwell Automation’s transformation results have been as follows: delivery gone up from 82 to 90 per cent, lead times reduced by fifty per cent, productivity increased more than five per cent and thirty per cent reduction in capex.
PTC AR by Vuforia studio provides powerful AR content creation for enterprise content creators and publishing solutions for industrial enterprises. Vuforia engine has use-cases in inspection and manufacturing operations, marketing and sales, presales manufacturing process services, training and project reviews.
Surface inspection systems for digital TV production by Samsung reduce human operator intervention in the production line, increase throughput and reduce errors in product inspection. System operation supports capturing TV surface image from high-resolution camera devices.
Samsung has also developed a post-processing system for an image captured by the camera to make it amenable to automatic detection. Automatic surface defect detection algorithm on a pre-processed image enables distinguishing of a real defect from a false one on the digital TV.
The connected cyber physical world has brought availability of information and ease of dissemination of information. Information-driven enterprises have enabled optimisation of resources. Leakage or waste can be minimised through connectivity, technology and transparency. For example, a 45kg coal wagon going from Jharkhand to NTPC plant results in at least thirty per cent wastage in resources. With the right technology connecting the point of source to the point of use, NTPC has to pay only for the coal that lands at the plant. This can be achieved through weighing the wagon at different locations through the whole passage, and this information connectivity can reduce under-invoicing and over-invoicing. This ultimately benefits the end consumer, reducing the price of per unit electricity.
Government and industry initiatives
By anticipating challenges before they arise is more likely to offer a successful digital transformation. Challenges experienced are lack of understanding, lack of scalability and poor workforce skills. Driving the next industrial revolution by reinventing 3D can help achieve immersive and easier designs and prototypes, and the final part of digital production.
Government initiatives for fuelling manufacturing leadership and innovations redefine and create new value opportunities.
To strengthen Make in India ecosystem with the adoption of smart technologies, Automation Industry Association and research institutes like IIT-Delhi and others have created a special-purpose vehicle, called Foundation for Smart Manufacturing (FSM), to take the emerging wave of smart technologies and adapt it with relevance to the needs of the Indian industry.
To facilitate, introduce and enlighten the industry with an evolved genre of quality-focused smart manufacturing, Department of Heavy Industry (DHI) supported by IITD-AIA Foundation for Smart Manufacturing (FSM), Federation of Indian Chambers of Commerce & Industry (FICCI) and IIoT India has been organising workshops to empower different industrialists to achieve the benefits of Industry 4.0.
Digitisation in the industrial manufacturing segment is about using capacity and a properly-calibrated information-driven solution to solve problems and reduce pain-points in the enterprise. And, early adopters of technology always benefit more by the industrial revolution digitisation.