The Industrial Internet of Things enhances manufacturing and industrial processes. Let us find out how.
The industry is a collection of three Ms: men, machines and materials. The primary function of the Internet of Things (IoT) is to integrate these effectively to meet industrial objectives. Several labs are, hence, researching various Internet technologies to apply to industrial situations.
The Industrial IoT (IIoT) promises to support a new era of smart industry, being a part of the IoT. The IoT is a network of intelligent computers, mobiles, gadgets and other objects that collect and share data. Collected data is sent to a central cloud-based service, where it is stored with other data and then shared with end users in a useful way. The IoT increases automation in homes, schools, stores and many other segments.
The IIoT has the potential to improve productivity across manufacturing sectors by integrating these with cloud computing, artificial intelligence (AI), deep learning and automation via the Internet. Hence, when the IoT is applied to the manufacturing industry, it is called IIoT.
Some key benefits of the IIoT are given below.
- Provides greater connectivity, efficiency and scalability
- Brings great savings in time and cost
- Improves safety and other operational efficiencies
- Improves the concept of Big Data
- Has openness and inter-operability, which means that it can connect all machines of an industry having different protocols in an effective manner
- Enhances supply chain efforts
- Provides green practices
- Provides high-quality control
A number of companies are implementing IIoT technologies by taking maximum advantage of intelligent and connected devices in their factories. One of the main characteristics of the industry is the presence of machines. Thus, any sector that makes use of machines can be termed as industry. Automobile, oil and gas, electrical and power, agriculture and hospitals are typical examples of such industries.
The IIoT connects processes from the factory floor to executive offices. Business leaders today are extensively using IIoT, as it helps them get a full view of how their enterprise is functioning. This helps them make better decisions.
In factories, devices and machines use different protocols and have different architectures. These might be sold by different vendors. Connecting these devices and machines, and providing security is the greatest challenge for the IIoT today.
Ignition is an excellent solution for this. It works on a cross platform, and is built on open source and standard IT technologies.
Companies want their data to be secure. Rapid increase in the number of sensors and other smart, connected devices has resulted in a parallel explosion of security attacks. This is another factor for the rise of the IIoT, since it provides data security by supporting several latest machine connectivity protocols.
Micro-robotics is another area for the IIoT’s improvement. Today, micro-robots are the size of dragon flies, which can be unleashed in huge numbers for gathering data. Newer processors, sensors, integrated wireless connectivity and other features can take the IIoT to greater heights.
Performance of sensors has improved so much over time that these tiny objects can measure several parameters (such as temperature, humdity, velocity, stress, torque, pressure, etc). These are now being integrated with the Internet in many interesting ways. With increased integration, it is now possible to incorporate and embed sensors inside chips. Such chips can support a number of peripherals such as machines, operators and the Internet.
Soon there may be raw materials and supplies that come with embedded tags, which certify the content and quality. This could reduce the time of inspection of incoming materials for the industry.
Today, a bank employee puts his thumb on a fingerprint reader to enter an Internet-based worksheet. In several colleges in India, advanced thumb readers are used for the purpose of attendance analysis.
Imagine a computer numerical control (CNC)-based components manufacturing industry. The same thumb reader may be attached to each CNC machine so that its access is limited to trained and authorised personnel only.
Inspection instruments like digital calipers and micrometers may soon come with tags so that data is automatically transferred to the cloud using analytics software. This could help achieve efficient quality control in the industry.
Today’s CNC machines and robots (using common communication protocols and standards) are not only capable of exchanging data among themselves but are intelligent enough (through the use of sensors and electronic circuits) to determine the health and performance of other machines (such as CNC drilling and milling machines) involved in the manufacturing cycle. These machines have self-correcting mechanisms, and can optimise themselves to avoid wastage and rejection. Thus, the IIoT has reshaped factories. Digitised manufacturing industries adopting the IIoT is referred to as Industry 4.0.
The IIoT is a common term for all hardware that work together through IoT connectivity to enhance manufacturing and other industrial processes. Industrial processes may be core (such as manufacturing and assembly) or non-core (such as inventory control, scheduling, cost analysis and billing).
However, the IIoT is facing many challenges including security of data. While designing the IIoT for a traditional industrial application, selection of proper protocols is necessary.
The network medium used (high-speed fibre, cable or cellular) is also an important factor in the IIoT. Cellular is gaining popularity in industrial spaces due to its simplicity and secured communication. Industrialists are now looking to create a simple, compact and cost-effective approach for IIoT communication.
Protocols to improve the IIoT
The IIoT follows several protocols for the industry. These can be grouped into two broad categories: client-server and publish-subscribe.
Machines that used edge-of-network technologies are now becoming outdated due to the IIoT. Protocols such as OPC UA and MQTT are quickly emerging as the standards for the IIoT, due to features like lightweight overhead, publish-subscribe model and bi-directional capabilities.
To create high-quality, efficient standard IIoT infrastructure, these protocols are essential. Some well-known IIoT protocols are described below.
OPC UA
OPC Unified Architecture (OPC UA) is the next-generation standard from The OPC Foundation. Classic OPC, a well-known standard for industry, provides a standard interface to communicate with PLCs. It is a client-server protocol, where the client can connect, browse, read and write to industrial equipment.
Highly secure, it is a good solution for tying PLC and sensor data into existing industrial applications like SCADA and manufacturing execution systems, where OPC and OPC UA connectivity are already available.
MQTT
Message Queue Telemetry Transport (MQTT) is a lightweight messaging protocol designed for volatile communication networks like cellular or satellite. It does not require high bandwidth or high-availability network connections. MQTT is preferred by hardware manufacturers due to its efficiency, security and scalability.
CoAP
Constrained Application Protocol (CoAP) is a specialised Web transfer protocol for use with constrained nodes and constrained networks in the IoT. It is designed for machine-to-machine (M2M) applications, such as smart energy and building automation.
AMQP
Advanced Messaging Queuing Protocol (AMQP) is an open standard for passing business messages between applications or organisations. It connects systems, feeds business processes with the information these need and reliably transmits onwards the instructions to achieve goals.
ZeroMQ
This is a high-performance messaging library for communication between applications or processes regardless of hardware or software. It can be an ideal IIoT protocol, provided the applications do not require high-performance or real-time operation.
STOMP
Streaming Text Oriented Messaging Protocol (STOMP) is similar to HTTP and is designed for interoperability of brokers.
A new lease of life to industries
The global IIoT market is expected to reach US$ 933.62 billion by 2025, according to a report by Grand View Research. Growing demand and adoption of cloud computing coupled with scalability of IPV6-3.4×1038 IP address are said to drive the market.
The global IIoT market exceeded US$ 100 billion in 2016 and is expected to grow at a CAGR of over 25 per cent from 2017 to 2025. The Asia-Pacific market is anticipated to outgrow the North American market and emerge as the highest revenue-generating region, with China spearheading the growth by the end of 2025.
In 2015, the Chinese government launched Made in China 2025 strategy. This project aims to increase China’s manufacturing innovation. The manufacturing sector of China has received in excess of US$ 1.5 billion with an objective to turn China into a manufacturing superhouse. As a result, the global IIoT industry is set to benefit from this.
The IIoT value chain across India
It might take a few years for the IIoT to be fine-tuned for wider industrial use. However, it can revolutionise business models by bringing smart manufacturing into play.
The manufacturing industry in India has shown phenomenal growth in the last decade. But India’s ranking as per Global Manufacturing Competitiveness Index has dropped from number 2 in 2014 to number 11 in 2016. A key reason for this is the lack of focus towards building a skilled workforce and the inability to establish modern technologies.
Automation in manufacturing companies in India is done through enterprise resource planning (ERP) systems. However, these are used for non-core activities such as inventory, ordering and invoicing. Core manufacturing processes are still labour-intensive. Use of CNC machines, programmable logical control (PLC) or supervisory control and data aquisition (SCADA) systems for automation are not common. Data from these systems remain in the common pool and are rarely used for process improvements.
The government of India’s Make in India initiative is designed to help manufacturing industries grow and compete in global markets. One such effort by Ministry of Heavy Industries is called Samarth Udyog Bharath 4.0. It is aimed to make Indian industries ready for Industry 4.0. It helps bring together industries in India with IIoT solution providers.
The IIoT is transforming manufacturing conditions in India. Apple India recently established a manufacturing IoT system, which is driving Industry 4.0. It aims to accelerate the industry to a new level, to transform economies and to open a new era of growth and competitiveness.
Tech Mahindra has been a member of General Electric (GE) Digital Alliance programme since 2016. The initiative is working towards building a digital ecosystem.
Tech Mahindra is also an early adopter of Predix platform, which is GE’s cloud-based platform as a service (PaaS) for the industrial Internet. Predix connects Tech Mahindra’s assets with data and analytics, with unprecedented speed and scale. It creates innovative solutions to address the needs of power, oil and gas, and transportation industries, among others.
In addition, Tech Mahindra is working on building solutions for smart city buildings. With over 100 Predix-trained experts, the company plans to invest in more than 1000 developers and architects for Predix platform in the next few years.
Connecting the IIoT to the automotive sector
As manufacturing and automotive sectors across the globe are getting ready for Industry 4.0, India is also gearing up for this change. This shift in the automotive and transportation industry benefits India immensely and will bring an entirely different paradigm.
In 2006, German government came up with Industry 4.0 to digitalise the manufacturing sector to increase productivity. While Industry 3.0 was simply an automation of isolated machines, Industry 4.0 demonstrated the timely use of all physical assets of the factory and their integration into the digital ecosystem with value chain partners.
Industry 4.0 is motivating technologists and entrepreneurs to develop new solutions with technological spins. A strong cyber security infrastructure is slowly building up in India, which is a major requirement for the IIoT ‘s capabilities.
By 2020, India is expected to become a major automobile manufacturing hub and the third largest market for automobiles in the world. As such, the automobile industry in India needs a dramatic increase in their level of digitalisation and investment in data analytics. As a result, IIoT technology has become a key enabler for bringing out change, which is driving a positive impact beyond the industry.
Industry 4.0 has its own road to follow for smart manufacturing. It needs support from segments like 3D printing, 3D sensors, social software, augmented reality (AR) and location awareness to enter the next era of smart production.
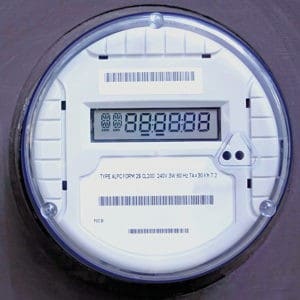
Automakers in India have already made headway into Industry 4.0. Bosch has initiated the implementation of Industry 4.0 in all of its 15 manufacturing facilities across India. The company is adopting national initiatives such as Make in India and Digital India to help its business move faster to market. It has collaborated with GE Digital for connected manufacturing and with SAP to develop cloud technology and software solutions.
Using the IIoT as a medium in the power sector
The IIoT provides great opportunities in the power sector across Asia-Pacific. GE predicts that US$ 1.3 trillion can be captured in the electricity value chain from 2016 to 2025 globally by the IIoT. Smart meters and smart thermostats are two important recognisable consumer-oriented applications of the IIoT in the power sector.
Older smart meters were Internet-connected devices for sending electricity consumption data to the concerned power utility. In newer versions, a variety of add-on services have been added. These services include energy management portal, net-metering, pre-paid electricity purchase, inventory control identification, voltage management to reduce losses and so on.
Burbank in California has benefitted greatly from the installation of advanced metering infrastructure. It has enabled about two per cent reduction in electricity usage per customer. Further, it has reduced response time to customer inquiries, brought 87 per cent reduction in field visits, improved reliability of grid with drop in system failure and more.
Smart thermostats are Internet-connected devices for measuring temperature and humidity inside homes or offices. These send collected data to the cloud. Smartphones can now do the job using the IIoT.
In addition, many machine learning applications have been developed for saving energy and user comfort. Applications of the IIoT in power sector mainly focus on power-generation plants (atomic, thermal, solar, wind, hydro-electric, etc) and in transmission and distribution grid.
In Asia, many grids are often unreliable. This is due to aged equipment, poor maintenance and, in many situations, un-upgraded power systems to meet high annual demand and growth rates. Investments in the IIoT for both existing and new equipment can significantly reduce unscheduled downtime of the grid, thereby improve reliability and reduce costs.
In conventional power plants, the IIoT can be used to balance production with the life of equipment and lifecycle cost of maintenance.
GE’s gas and coal power plant captures the unique characteristics of the IIoT. Its digital technologies, when applied to the new coal and gas fired power plant, have increased fuel efficiencies by three per cent and power output by two per cent.
In a non-conventional wind power plant, the IIoT can be used for reducing wake losses by adjusting pitch and yaw angles of individual turbines, controlling stress and fatigue loading within acceptable limits, and setting individual turbines in wind farms to optimum level-to-local conditions.
The IIoT orientation across oil and gas industries
Asset-intensive industries like oil and gas, mining, construction, energy, rail and logistics face many challenges. These must be solved to improve reliability, operational performance and achieve operational objectives.
In the oil and gas industry, asset monitoring is critical, during oil exploration to ensure expensive rigs are in working order. Parts and corrective maintenance, and timely oil pumping is necessary too. Equipment used should meet various health and environmental regulations. As a result, gathering of data is extremely essential during transmission from exploration to production sites. In general, an oil and gas company must record all details of its assets and all activities of those assets to maintain and maximise site productivity and asset performance.
As a part of IIoT initiatives, in Eagle Ford region of North America, a new suite of technologies associated with the IoT enabled oil rigs to produce 65 times more efficiently in 2013.
Despite margin pressure and capital constraints, the oil and gas industry has many reasons to invest in this front-end IoT technology. Gathering of geo-technical seismic related data for reserves/deposits of oil and gas need digital technology. The IIoT, which is a new approach for Big Data and predictive analytics, certainly is a boon here. Compressors, turbines and other gas transmission equipment are becoming smarter due to the application of IIoT technologies.
As far as safety and regulatory issues are concerned, IoT solutions can greatly manage remote facilities and tank collection sites in real-time frameworks.
In oil-extraction facilities and tank collection sites, oil and gas companies must manage spills, emergency shut downs and regulatory issues. Most of these are remote field operations. Today, sensors can help with predictive maintenance, by reaching problem areas and gathering information about pressure and flow rates. Once problems are identified, corrective actions can be taken.
A prominent problem facing gas wells is liquid loading, which is the inability of gas to remove liquids being produced in the well bore. A hole is drilled for the purpose of exploration. This problem occurs when velocity of the gas being produced drops below critical levels. Accumulated liquid at one stage ceases production. Early prediction is necessary in this case. This is where the IIoT comes into play.
The IIoT setting new standards
The main requirements of the industry are capital and demand for product. As such, the IIoT is still a dream for small-scale industries. However, this technology can add new colours to the industry. Companies often face problems like market speed, volatility and disruptive technologies. Those using the IIoT can significantly improve safety, efficiency and profitability of their products.
The IIoT enhances manufacturing and industrial processes. While communicating with real-time data, smart machines are better than humans. Real-time data increases efficiency, solves problems, saves time and money, and supports business intelligence efforts.
Vinayak Ramachandra Adkoli is BE in industrial production. He was lecturer in mechanical department for 10 years in three different polytechnics. Now, he is a freelance writer and cartoonist