Micro-electro-mechanical system (MEMS) sensors enable advanced automation and the Industrial Internet of Things (IIoT) by advanced industrial sensing. Deepshikha Shukla of Electronics For You discusses the same with Vishal Goyal, senior technical marketing manager, Analog and MEMS Group, ASEAN-ANZ and India, STMicroelectronics (ST).
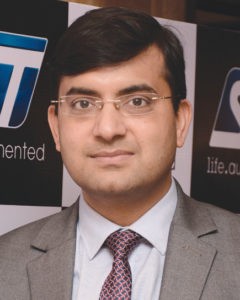
Q. How has the semiconductor market grown in terms of MEMS sensors?
A. The first MEMS wave came with the mobile age, which helped smartphones advance at a rapid pace. Then, the cloud and the IoT ages flourished. Now, high-accuracy MEMS sensors are driving automation for the fourth industrial revolution, or Industry 4.0.
Industry 4.0 involves connected devices, distributed computing, analytics and predictive maintenance. It has wide applications in the fields of defence, robotics, oil and gas, energy and agriculture, among others.
In the last 20 years, ST’s portfolio of MEMS sensors has evolved to accelerometers, gyroscopes, inertial modules, magnetometers, pressure sensors, microphones, humidity and temperature sensors.
Q. How will machine monitoring systems evolve for Industry 4.0?
A. Accuracy, longevity and reliability are the key features provided by MEMS to support smart industry. For example, an inclinometer can adjust antenna tilt angle on its own, as in a solar tracker.
Sensors play a major role in smart industry by predicting the type of failure in machines, and informing relevant authorities, if needed.
Machines are connected so that their status can be sent to the cloud wirelessly, directly or routed through a gateway using MEMS sensors. This way, everything can be built on the cloud. Machine monitoring through sensors reduces the cost of testing by large machines.
Q. Can you talk about one emerging technology for smart industry?
A. An emerging technology for smart industry is IO-Link, which is a way for machines to communicate with each other. IO-Link has a standard that is more customised to machines. Here, you can not only see what a sensor is doing but also give feedback. It is a two-way communication system using sensors.
IO-Link has many uses from an industrial perspective, which have all been taken care of in IO-Link standard. Now, communication between machines and cloud can also happen through IO-Link.
Q. Please share one latest technology solution for the IIoT?
A. For Industry 4.0, there are products that can be applied in early-failure-detection and predictive-maintenance systems where vibration, temperature, pressure, sound and acoustics analyses are needed.
For example, ST’s SensorTile is a low-power, small form factor, ready-to-use onboard system, which is fitted with 3-axis magnetometer, 3-axis digital gyroscope, microphone, and sensors for relative humidity, ambient light and temperature.
Q. How can predictive analysis of faulty motors be achieved with this setup?
A. A vibration-based frequency measurement setup for predictive analysis of a faulty motor uses sensors embedded on top of the motor. Sensors measure high-frequency signals that are generated, and send these over IO-Link. Frequency signals of a faulty motor are measured and compared with reference signals of a working motor using simulation software.
For industrial applications, we have a predictive maintenance tool with a compact, low-voltage, dual-motor-control evaluation board for conditional monitoring and early motor failure detection, as well as eSIM/machine-to-machine solutions for industrial and telematics applications. IO-Link enables communication between different end devices and sensors for industrial use.
Q. What are some popular MEMS sensors for smart industry?
A. Conditional monitoring systems include microcontroller for processing, BLE (BlueNRG-2) and RF sub-Ghz (S2-LP) for connectivity, power ICs for power management, MEMS microphones, touchscreen controllers, and sensors such as humidity, pressure, proximity and temperature.
Some of our popular products are IIS3DHHC, ISM330DLC and ISM303DAC.